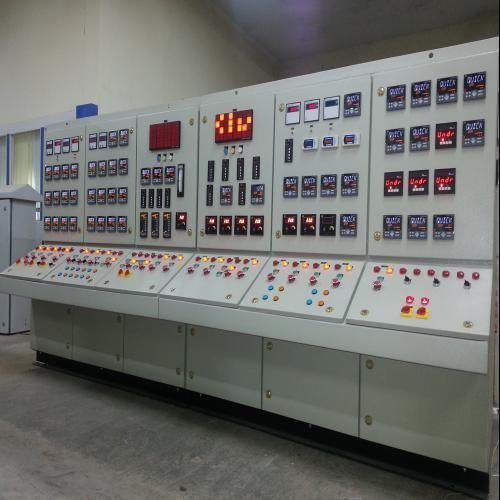
Process control panel
In most modern processing plants, production equipment and systems incorporate at least some degree of automation. Sometimes it comes integrated with packaged equipment from original equipment manufacturer (OEM) vendors, and other times the controls are designed by engineering firms and systems integrators (SIs). Control panels are usually assembled in a shop dedicated to this work, and they are then factory-installed on OEM equipment or shipped to the field for “stick built” installations.
Designing the electrical, instrumentation and control (EIC) systems and panels supporting this widespread automation is a specialty. But end users of all types in a range of disciplines can benefit from understanding some of the fundamentals involved with designing and building a typical industrial control panel
Requirements
While some types of instrumentation and industrial control components do not require a protective housing, it is more common for most EIC devices to be installed in control panels of some sort. Control panels protect these devices from local environmental conditions — heat, cold, moisture, contaminants — and they also protect workers from electrical voltages.
Typical industrial control panels fulfill many roles including some or all of the following:
- Providing a suitable environment for control devices.
- Keeping personnel safe and away from these devices.
- Performing power distribution and voltage conversion.
- Offering a centralized and maintainable location for programmable logic controllers (PLCs), input/output (I/O) modules, human-machine interfaces (HMIs) and related components.
- Supporting motor control devices like variable frequency drives (VFDs) and servo/motion controls.
- Housing communications and connectivity systems.
Utilities, signals and components
Some fundamentals for control panel design include electrical power needs, I/O and networking signals, and the components needed to perform these functions. Designers must be fully versed in these concepts, but end users should know enough to coordinate what is available at the site with new control panels, including these basic requirements:
Incoming power circuit voltage and amps and how this affects the short circuit current rating (SCCR) requirements. Sometimes there will need to be multiple incoming power circuits, or perhaps a 480VAC 3-phase circuit that will be transformed and/or converted to other lower voltages within the control panel.
Discrete I/O signal levels (120VAC or 24VDC sourced by the control panel, or dry contacts for interfacing with other systems).
Analog I/O signal levels (4-20mA, 0-10VDC, or other).
Networking media and protocols (such as serial, fieldbus, or Ethernet; and Modbus RTU, PROFIBUS, EtherNet/IP, etc.).
Motor voltages and loads (FLA).
As components are selected, panel designers often find it helpful to create a block diagram showing the relationship of these devices. Once the components are selected, a rough approximation of the layout must be created so that the enclosure can be sized.
Once the size is known, it is necessary to choose an enclosure suitable for the environment. Painted carbon steel is standard and economical, but damp areas or locations with washdown requirements and exposure to chemicals may require stainless steel or fiberglass options. Food, beverage and pharmaceutical installations may require special sanitary enclosures that resist harboring contamination
Testing
Thorough testing is necessary to ensure proper control panel assembly and functionality. As assembly is completed, the panel shop should provide proof that they have verified the parts used, the overall arrangement, proper tags and correct grounding/bonding. They should demonstrate that they have performed point-to-point wiring tests, progressively powered-on interior elements and checked basic circuit and I/O signals.
The most advanced tests will go beyond these basics to exercise PLC program functionality and demonstrate communications to VFDs, HMIs and other intelligent devices. This type of testing is more practical for control panels installed on OEM equipment, but many tests can be performed on control panels destined for stick-built installation.
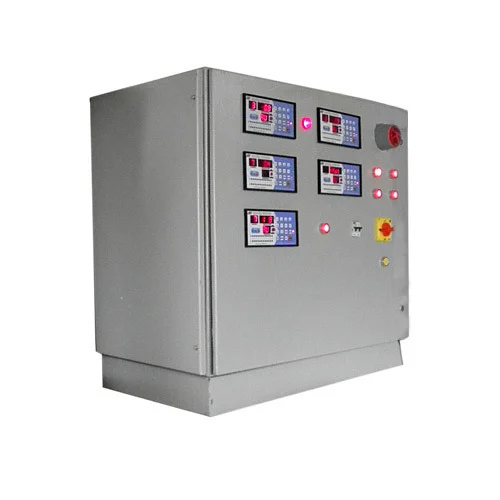
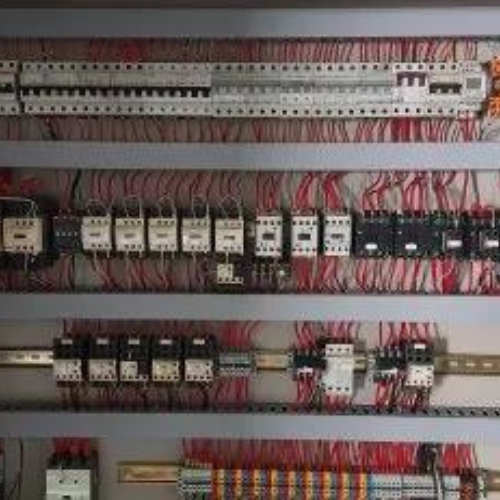
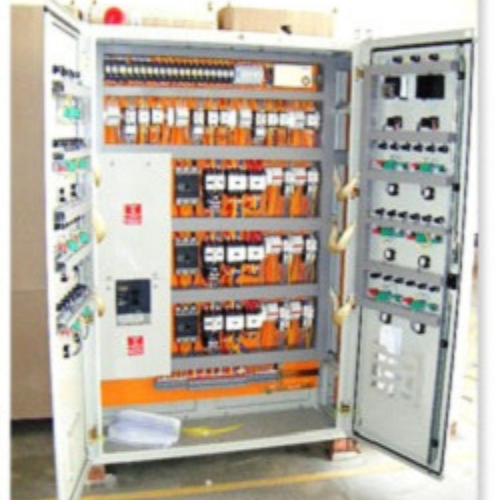